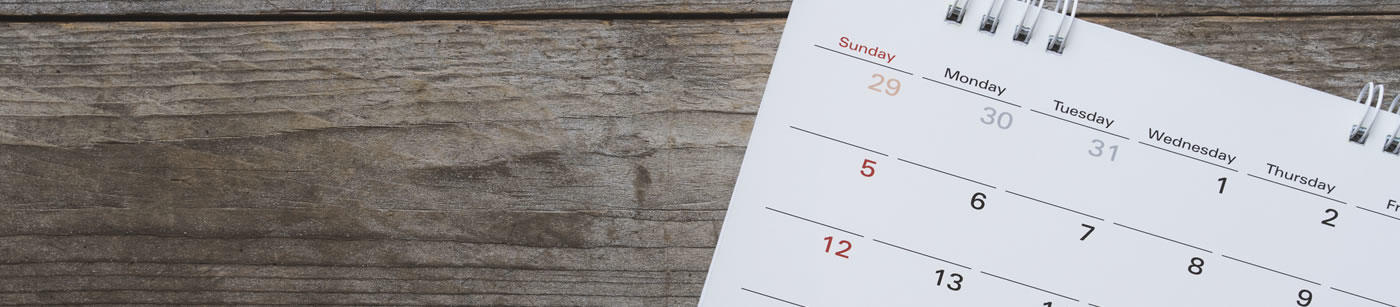
Actualités
Interview d'exploitant - La politique de décarbonation d’Eramet
Le 10|11|2020
Publié le 12|11|2020
En quelques années, ERAMET est passé d’une simple optimisation des achats d’énergie à une politique exigeante d’efficacité énergétique et de décarbonation. Jean-Philippe Letellier, Coordinateur « Energie et Climat » d’ERAMET, nous raconte ce véritable projet de transformation de l’entreprise, qui a renouvelé la « façon de penser » la production.
ALLICE : Vous êtes chez ERAMET depuis 1988 et plus particulièrement en charge de la maîtrise de l’énergie depuis 2012. Comment avez-vous vu évoluer la prise en compte de ce sujet dans votre entreprise ?
Jean-Philippe LETELLIER : Notre métier, la transformation des minerais, est très énergivore. Historiquement, l’aspect énergétique était vu avec une approche « production » : l’énergie était une nécessité et ne devait pas être un frein. Certes, il fallait l’optimiser, pour des questions de coûts, de concurrence internationale… mais comme toutes les autres dimensions de nos process de production.
A partir de 2005, avec la montée du coût de l’énergie, toujours de plus en plus chère et de plus en plus rare, il y a eu une prise de conscience. Pendant 5 ou 6 ans, les actions déployées ont alors visé à réduire la consommation d’énergie de nos sites. Nous avons recruté un expert, pour réaliser des audits techniques et suggérer des plans de progrès aux usines.
C’est en 2011, avec la publication de la norme ISO 50001 qu’il y a eu un premier basculement : on disposait alors d’un outil sur lequel les sites pouvaient s’appuyer pour structurer leur démarche. Jusqu’en 2017, on les a incités à s’inspirer de la norme et, s’ils le souhaitaient, à aller jusqu’à la certification. Mais ce n’était pas encore une obligation formelle de la part du groupe.
Comment en êtes-vous venus à adopter une politique centralisée au niveau du groupe ?
En 2014, la réglementation sur les audits obligatoires, dont les entreprises certifiées ISO 50001 sont exemptées, a marqué une nouvelle étape. Après une première phase encore basée sur le volontariat, nous nous sommes engagés en 2017 sur une obligation pour nos sites consommant plus de 200 GWh par an de se certifier avant 2020, et nous avons adopté progressivement des exigences de plus en plus fortes en la matière. En 2019, le groupe a pris un nouvel engagement formel significatif : réduire ses émissions de CO2 de 26% d’ici 2023.
En quelques années, on a assisté à un passage de la gestion de l’énergie comme une matière première, dont l’optimisation relevait plutôt du domaine des achats pour réduire les coûts, à une véritable démarche de sobriété structurée autour de l’ISO 50001 et de la réduction des émissions de GES.
Il s’agit d’un vrai projet de transformation de la « façon de penser » l’énergie : comment avez-vous conduit ce changement en interne ?
En 2018, le groupe a créé une direction énergie et climat, dont je fais partie, elle-même directement rattachée à la direction de la stratégie. Mon n+3, c’est le PDG du groupe, cela a un sens ! Le sujet est vraiment porté au plus haut niveau.
Sur le terrain, le changement a été conduit avec succès, car nous avons été très pragmatiques. Le principal témoignage que je souhaite partager, c’est que la démarche doit s’appuyer sur ce qui existe pour amener des améliorations, et ne surtout pas « plaquer des choses toutes faites », imposées par la direction centrale qui ne prendraient pas en compte les spécificités de chaque usine. Dès 2005, l’auditeur interne qui a commencé à conseiller les sites a adopté cette méthode. En allant sur le terrain, il a vu la différence de maturité existante d’un site à l’autre, d’un pays à l’autre. Il faut impérativement faire coïncider l’idéal à atteindre, la norme, avec la réalité du terrain pour trouver le bon cheminement de chaque site. Il n’existe pas a priori de solutions standardisées pour tous.
La résistance au changement, on l’a connue : il est parfois plus simple pour un consultant externe d’être écouté que pour un auditeur interne. Mais grâce à ce pragmatisme, depuis 2015 environ, tout le monde se sent concerné par la volonté d’amélioration.
Aujourd’hui, notre organisation est consolidée autour de 4 personnes en central et d’un correspondant par site. Nous avons des rapports mensuels pour partager et progresser, et nous avons été invités en comité exécutif à présenter notre programme d’améliorations sur plusieurs années. Ce sont bien tous les niveaux managériaux de l’entreprise qui sont parties prenantes.
Vous insistez sur la dimension « compétences internes » pour mener la démarche. Quels sont les atouts qui vous ont conduit à ce choix ?
Je suis moi-même très impliqué dans les sujets « énergie » à différents niveaux : groupes d’expert, commission de normalisation, enseignant à l’INSA Centre Val de Loire… et j’ai poussé pour que le groupe intègre les compétences en interne. Pour notre activité, cette dimension est stratégique, et il me semblait que c’était une véritable opportunité pour nous d’être autonomes sur le sujet. Cela permet non seulement de mieux prendre en compte les spécificités des sites, comme je viens de l’évoquer, mais aussi de s’inscrire dans la durée, contrairement à une mission de consultant, forcément limitée dans le temps. Lorsque nous avons lancé la démarche ISO 50001, nous étions déjà certifiés ISO 14001, donc la culture d’entreprise était prête à intégrer une nouvelle démarche de système de management, les équipes étaient sensibilisées et pouvaient monter en compétences. Comme nous avons une quarantaine de sites dans le monde, en 2014, nous avons embauché un apprenti et formé 4 auditeurs. Peu à peu, de nouveaux collaborateurs se sont formés, on a pu lancer des audits croisés…
A ne pas négliger non plus : la capacité à progresser que procure le fait de transmettre ses compétences à des jeunes. Cela nous oblige à nous réinterroger sur nos méthodes et à bien toujours se rappeler les fondamentaux.
Vous êtes un groupe international et c’est une politique au niveau du groupe. Quels sont les enseignements issus des autres pays ? Fixez-vous les mêmes objectifs, par exemple de réduction de 26% des émissions de GES, à tous les sites ou est-ce un objectif central, réparti selon les capacités des différentes usines ?
Effectivement, nous avons des sites partout dans le monde. Pendant très longtemps, les pays européens ont été moteurs, puisque le système EU ETS les oblige à être pro-actifs en matière d’efficacité énergétique. Tous les pays n’ont pas atteint le même niveau de maturité sur ces problématiques et il serait peu réaliste d’imposer le même niveau d’effort à un site en Norvège qu’à un site en Afrique Subsaharienne. Ici encore, c’est le pragmatisme qui l’emporte, avec un objectif de 26% de réduction des GES au niveau du groupe, mais une adaptation à la réalité terrain pour chaque usine.
D’une manière générale, nous actionnons deux leviers pour progresser :
Vos objectifs de certification de tous vos sites avant fin 2020 sont-ils atteints ?
Sans la Covid-19, ils l’auraient sûrement été ! Il ne nous en reste que deux : l’un aux Etats-Unis, où la situation sanitaire a vraiment été bloquante pour faire avancer le dossier, l’autre au Gabon, où le site est prêt, mais il est très complexe avec les quarantaines qui sont imposées de faire venir un auditeur…
Pour contribuer au financement de vos actions, vous appuyez-vous sur les CEE ?
Très peu, car il n’a longtemps pas été possible de faire appel à ce mécanisme pour les sites soumis à l’EU ETS, ce qui était le cas pour nous. De ce fait, nous ne nous sommes pas suffisamment structurés en interne pour cela. Aujourd’hui, les règles de l’EU ETS sont assouplies et il y a quelques sujets intéressants que nous étudions.
Pour un groupe comme le vôtre, les investissements pour l’efficacité énergétique et la décarbonation sont conséquents. Comment réalisez-vous vos arbitrages budgétaires, vos choix de technologies… ?
A chaque fois, on regarde les 3 axes évoqués, qui sont donc : l’optimisation des achats, axe historique, puis l’amélioration de l’efficacité énergétique et enfin la réduction des GES. On a défini un coût interne du CO2 pour challenger nos solutions technico-économiques, ce qui nous amène, que ce soit au niveau des procédés ou des achats, à trouver des points d’équilibre qui ne sont pas toujours ceux qui auraient été choisis spontanément.
En intégrant ce nouveau facteur, on s’aperçoit qu’il est parfois globalement plus rentable de faire tourner un four à 90% qu’à son taux maximum, car l’économie d’énergie et d’émissions de GES en vaut largement la peine. On recherche donc en permanence le meilleur compromis technico-économique à la tonne produite.
C’est un changement de fond : aujourd’hui, on peut décider de produire moins pour améliorer le ratio rentabilité économique / énergie / carbone.
Aujourd’hui, on parle beaucoup de numérique, d’intelligence artificielle, de data… Comment intégrez-vous ces nouvelles technologies dans votre approche ?
Nous avons toujours utilisé largement des logiciels parfois complexes pour piloter nos installations, complexes elles aussi ! Nous développions déjà beaucoup de choses en interne, et depuis 2016, ici aussi, il y a eu une évolution notable : le groupe a créé une direction de la transition numérique. Nous travaillons ensemble sur ces sujets, nous créons des POC (Proof of Concept), puis, quand l’un d’eux fonctionne sur un site, nous le déclinons.
De nouveau, vous avez fait le choix de l’internalisation des compétences ?
Effectivement ! Il y a certes des sociétés spécialisées, très compétentes, qui nous ont démarchés, mais nous avons deux cas de figures :
- en fonction du sens du vent, on doit utiliser telle ou telle catégorie de fioul ;
- en fonction de la météo, on peut faire appel ou non au photovoltaïque ;
- en fonction du niveau d’eau du barrage, on compte ou pas sur l’hydroélectricité !
C’est un cas très précis, difficilement transposable sans adaptation conséquente à un autre site. Il s’est tout à fait prêté au développement, avec des start-ups, d’un outil d’aide à la décision efficace, à partir de l’ensemble de ces données d’entrée.
Un mot de conclusion ?
Depuis un an, les clients nous demandent l’analyse du cycle de vie de nos produits. Ils se préoccupent du contenu carbone de ce qu’ils achètent. Cela compte pour décrocher des marchés et a un véritable impact : il nous arrive désormais de choisir des procédés en fonction du critère climatique. C’est un changement fondamental dans notre manière de réfléchir, les prémisses d’une évolution notable du marché vers une industrie bas-carbone.
En complément :
ALLICE : Vous êtes chez ERAMET depuis 1988 et plus particulièrement en charge de la maîtrise de l’énergie depuis 2012. Comment avez-vous vu évoluer la prise en compte de ce sujet dans votre entreprise ?
Jean-Philippe LETELLIER : Notre métier, la transformation des minerais, est très énergivore. Historiquement, l’aspect énergétique était vu avec une approche « production » : l’énergie était une nécessité et ne devait pas être un frein. Certes, il fallait l’optimiser, pour des questions de coûts, de concurrence internationale… mais comme toutes les autres dimensions de nos process de production.
A partir de 2005, avec la montée du coût de l’énergie, toujours de plus en plus chère et de plus en plus rare, il y a eu une prise de conscience. Pendant 5 ou 6 ans, les actions déployées ont alors visé à réduire la consommation d’énergie de nos sites. Nous avons recruté un expert, pour réaliser des audits techniques et suggérer des plans de progrès aux usines.
C’est en 2011, avec la publication de la norme ISO 50001 qu’il y a eu un premier basculement : on disposait alors d’un outil sur lequel les sites pouvaient s’appuyer pour structurer leur démarche. Jusqu’en 2017, on les a incités à s’inspirer de la norme et, s’ils le souhaitaient, à aller jusqu’à la certification. Mais ce n’était pas encore une obligation formelle de la part du groupe.
Comment en êtes-vous venus à adopter une politique centralisée au niveau du groupe ?
En 2014, la réglementation sur les audits obligatoires, dont les entreprises certifiées ISO 50001 sont exemptées, a marqué une nouvelle étape. Après une première phase encore basée sur le volontariat, nous nous sommes engagés en 2017 sur une obligation pour nos sites consommant plus de 200 GWh par an de se certifier avant 2020, et nous avons adopté progressivement des exigences de plus en plus fortes en la matière. En 2019, le groupe a pris un nouvel engagement formel significatif : réduire ses émissions de CO2 de 26% d’ici 2023.
En quelques années, on a assisté à un passage de la gestion de l’énergie comme une matière première, dont l’optimisation relevait plutôt du domaine des achats pour réduire les coûts, à une véritable démarche de sobriété structurée autour de l’ISO 50001 et de la réduction des émissions de GES.
Il s’agit d’un vrai projet de transformation de la « façon de penser » l’énergie : comment avez-vous conduit ce changement en interne ?
En 2018, le groupe a créé une direction énergie et climat, dont je fais partie, elle-même directement rattachée à la direction de la stratégie. Mon n+3, c’est le PDG du groupe, cela a un sens ! Le sujet est vraiment porté au plus haut niveau.
Sur le terrain, le changement a été conduit avec succès, car nous avons été très pragmatiques. Le principal témoignage que je souhaite partager, c’est que la démarche doit s’appuyer sur ce qui existe pour amener des améliorations, et ne surtout pas « plaquer des choses toutes faites », imposées par la direction centrale qui ne prendraient pas en compte les spécificités de chaque usine. Dès 2005, l’auditeur interne qui a commencé à conseiller les sites a adopté cette méthode. En allant sur le terrain, il a vu la différence de maturité existante d’un site à l’autre, d’un pays à l’autre. Il faut impérativement faire coïncider l’idéal à atteindre, la norme, avec la réalité du terrain pour trouver le bon cheminement de chaque site. Il n’existe pas a priori de solutions standardisées pour tous.
La résistance au changement, on l’a connue : il est parfois plus simple pour un consultant externe d’être écouté que pour un auditeur interne. Mais grâce à ce pragmatisme, depuis 2015 environ, tout le monde se sent concerné par la volonté d’amélioration.
Aujourd’hui, notre organisation est consolidée autour de 4 personnes en central et d’un correspondant par site. Nous avons des rapports mensuels pour partager et progresser, et nous avons été invités en comité exécutif à présenter notre programme d’améliorations sur plusieurs années. Ce sont bien tous les niveaux managériaux de l’entreprise qui sont parties prenantes.
Vous insistez sur la dimension « compétences internes » pour mener la démarche. Quels sont les atouts qui vous ont conduit à ce choix ?
Je suis moi-même très impliqué dans les sujets « énergie » à différents niveaux : groupes d’expert, commission de normalisation, enseignant à l’INSA Centre Val de Loire… et j’ai poussé pour que le groupe intègre les compétences en interne. Pour notre activité, cette dimension est stratégique, et il me semblait que c’était une véritable opportunité pour nous d’être autonomes sur le sujet. Cela permet non seulement de mieux prendre en compte les spécificités des sites, comme je viens de l’évoquer, mais aussi de s’inscrire dans la durée, contrairement à une mission de consultant, forcément limitée dans le temps. Lorsque nous avons lancé la démarche ISO 50001, nous étions déjà certifiés ISO 14001, donc la culture d’entreprise était prête à intégrer une nouvelle démarche de système de management, les équipes étaient sensibilisées et pouvaient monter en compétences. Comme nous avons une quarantaine de sites dans le monde, en 2014, nous avons embauché un apprenti et formé 4 auditeurs. Peu à peu, de nouveaux collaborateurs se sont formés, on a pu lancer des audits croisés…
A ne pas négliger non plus : la capacité à progresser que procure le fait de transmettre ses compétences à des jeunes. Cela nous oblige à nous réinterroger sur nos méthodes et à bien toujours se rappeler les fondamentaux.
Vous êtes un groupe international et c’est une politique au niveau du groupe. Quels sont les enseignements issus des autres pays ? Fixez-vous les mêmes objectifs, par exemple de réduction de 26% des émissions de GES, à tous les sites ou est-ce un objectif central, réparti selon les capacités des différentes usines ?
Effectivement, nous avons des sites partout dans le monde. Pendant très longtemps, les pays européens ont été moteurs, puisque le système EU ETS les oblige à être pro-actifs en matière d’efficacité énergétique. Tous les pays n’ont pas atteint le même niveau de maturité sur ces problématiques et il serait peu réaliste d’imposer le même niveau d’effort à un site en Norvège qu’à un site en Afrique Subsaharienne. Ici encore, c’est le pragmatisme qui l’emporte, avec un objectif de 26% de réduction des GES au niveau du groupe, mais une adaptation à la réalité terrain pour chaque usine.
D’une manière générale, nous actionnons deux leviers pour progresser :
- Nous augmentons le volume de nos activités faiblement émettrices ;
- Sur une même activité, nous demandons aux usines de réduire les MWh par tonne produite, mais les objectifs de réduction prennent en compte les différents métiers
Vos objectifs de certification de tous vos sites avant fin 2020 sont-ils atteints ?
Sans la Covid-19, ils l’auraient sûrement été ! Il ne nous en reste que deux : l’un aux Etats-Unis, où la situation sanitaire a vraiment été bloquante pour faire avancer le dossier, l’autre au Gabon, où le site est prêt, mais il est très complexe avec les quarantaines qui sont imposées de faire venir un auditeur…
Pour contribuer au financement de vos actions, vous appuyez-vous sur les CEE ?
Très peu, car il n’a longtemps pas été possible de faire appel à ce mécanisme pour les sites soumis à l’EU ETS, ce qui était le cas pour nous. De ce fait, nous ne nous sommes pas suffisamment structurés en interne pour cela. Aujourd’hui, les règles de l’EU ETS sont assouplies et il y a quelques sujets intéressants que nous étudions.
Pour un groupe comme le vôtre, les investissements pour l’efficacité énergétique et la décarbonation sont conséquents. Comment réalisez-vous vos arbitrages budgétaires, vos choix de technologies… ?
A chaque fois, on regarde les 3 axes évoqués, qui sont donc : l’optimisation des achats, axe historique, puis l’amélioration de l’efficacité énergétique et enfin la réduction des GES. On a défini un coût interne du CO2 pour challenger nos solutions technico-économiques, ce qui nous amène, que ce soit au niveau des procédés ou des achats, à trouver des points d’équilibre qui ne sont pas toujours ceux qui auraient été choisis spontanément.
En intégrant ce nouveau facteur, on s’aperçoit qu’il est parfois globalement plus rentable de faire tourner un four à 90% qu’à son taux maximum, car l’économie d’énergie et d’émissions de GES en vaut largement la peine. On recherche donc en permanence le meilleur compromis technico-économique à la tonne produite.
C’est un changement de fond : aujourd’hui, on peut décider de produire moins pour améliorer le ratio rentabilité économique / énergie / carbone.
Aujourd’hui, on parle beaucoup de numérique, d’intelligence artificielle, de data… Comment intégrez-vous ces nouvelles technologies dans votre approche ?
Nous avons toujours utilisé largement des logiciels parfois complexes pour piloter nos installations, complexes elles aussi ! Nous développions déjà beaucoup de choses en interne, et depuis 2016, ici aussi, il y a eu une évolution notable : le groupe a créé une direction de la transition numérique. Nous travaillons ensemble sur ces sujets, nous créons des POC (Proof of Concept), puis, quand l’un d’eux fonctionne sur un site, nous le déclinons.
De nouveau, vous avez fait le choix de l’internalisation des compétences ?
Effectivement ! Il y a certes des sociétés spécialisées, très compétentes, qui nous ont démarchés, mais nous avons deux cas de figures :
- Sur nos process cœur de métier, cela nous pose problème d’externaliser : nous préférons avoir la maîtrise des aspects stratégiques et une forte volonté de garder l’expertise en interne. Il y a une dimension de confidentialité, et, sur ces sujets nouveaux, les questions de propriété intellectuelle restent sensibles. Si une entreprise utilise nos données et cas concrets pour créer un algorithme : à qui appartient le brevet ? Au propriétaire des données ou au créateur de l’algorithme ? Comment sont utilisées nos données ? A qui servent-elles ? Il ne faut pas oublier, pour nous, l’énergie représente 30% de notre prix de revient, l’enjeu est donc crucial.
- Les utilités, qui, chez nous, représentent environ 2% de nos consommations. Même avec des sociétés performantes qui nous feraient gagner 10 ou 15% sur ces consommations-là, cela, à ce stade, ne vaut pas la peine. Quand nous aurons fait le tour de toutes les autres économies possibles, peut-être y penserons-nous, mais nous avons encore des marges de progression sur les procédés fortement consommateurs.
- en fonction du sens du vent, on doit utiliser telle ou telle catégorie de fioul ;
- en fonction de la météo, on peut faire appel ou non au photovoltaïque ;
- en fonction du niveau d’eau du barrage, on compte ou pas sur l’hydroélectricité !
C’est un cas très précis, difficilement transposable sans adaptation conséquente à un autre site. Il s’est tout à fait prêté au développement, avec des start-ups, d’un outil d’aide à la décision efficace, à partir de l’ensemble de ces données d’entrée.
Un mot de conclusion ?
Depuis un an, les clients nous demandent l’analyse du cycle de vie de nos produits. Ils se préoccupent du contenu carbone de ce qu’ils achètent. Cela compte pour décrocher des marchés et a un véritable impact : il nous arrive désormais de choisir des procédés en fonction du critère climatique. C’est un changement fondamental dans notre manière de réfléchir, les prémisses d’une évolution notable du marché vers une industrie bas-carbone.
En complément :
- Jean-Philippe Letellier participe à l’e-table ronde « EMS » organisée par ALLICE le 17 novembre 2020 en visio. Inscription ici.
- Eramet a participé à l’étude « Etat de l’art sur les Energy Management Systems dans l’industrie » réalisée par Enea Consulting pour ALLICE en juillet 2019, en partageant notamment son expérience avec le fournisseur Optimistik pour le site d’Eramet Research. Plus d’infos ici.
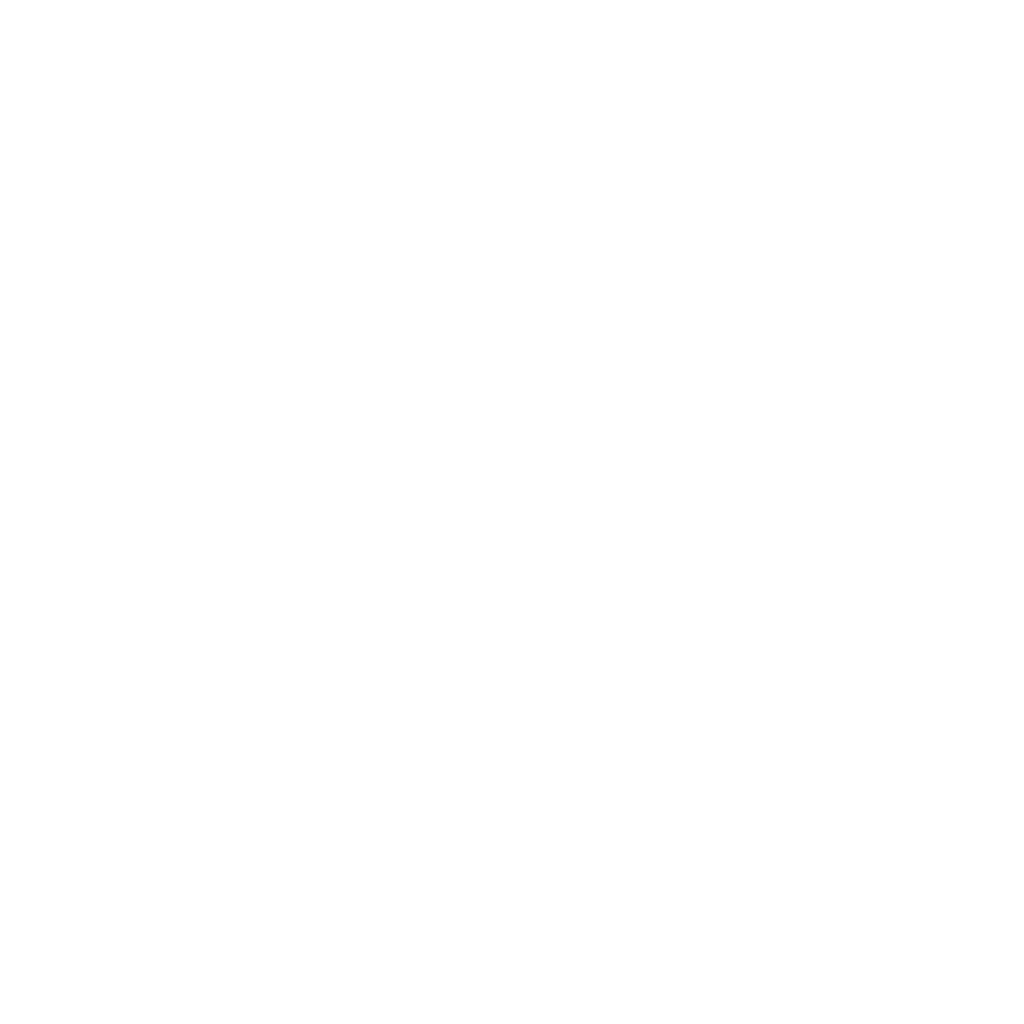
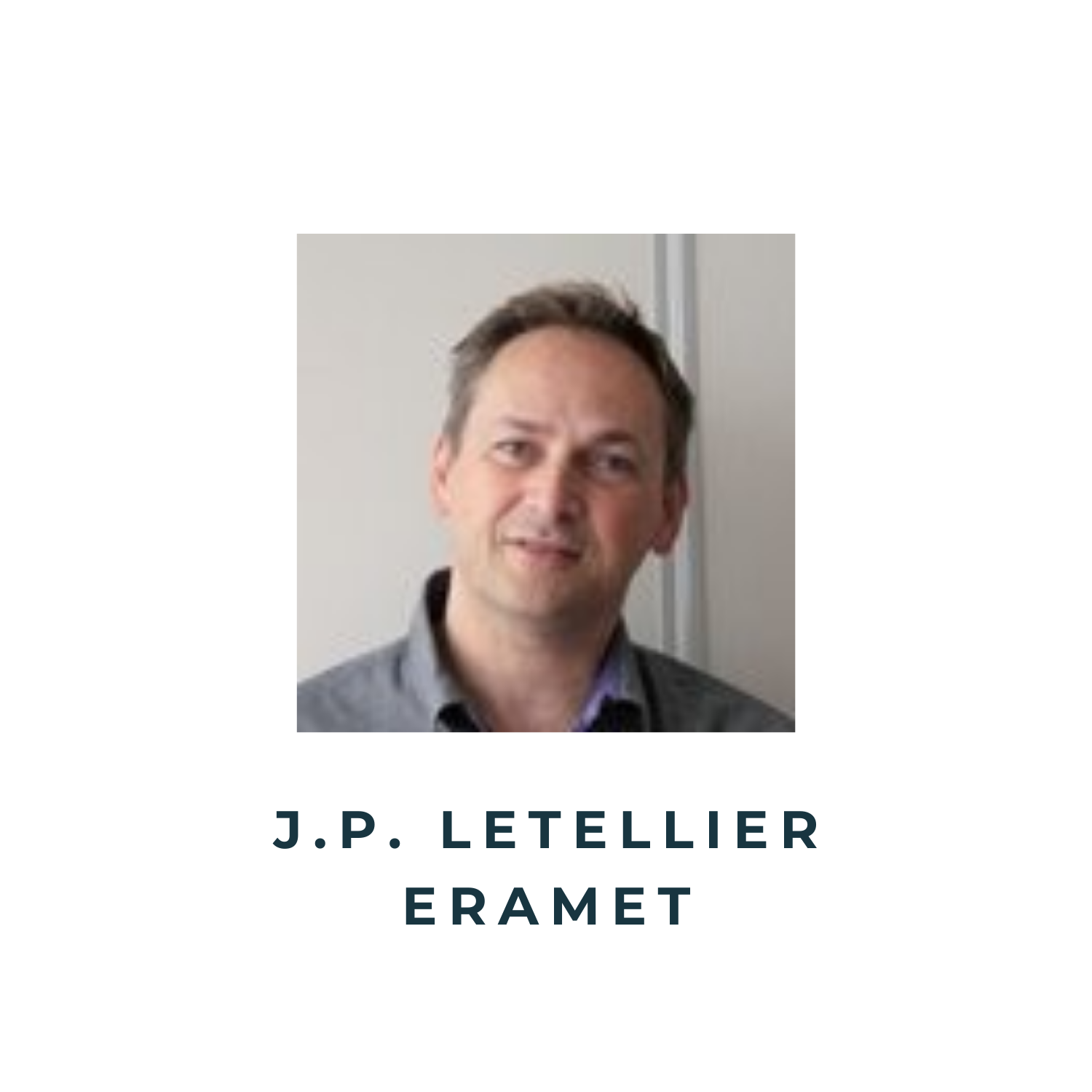