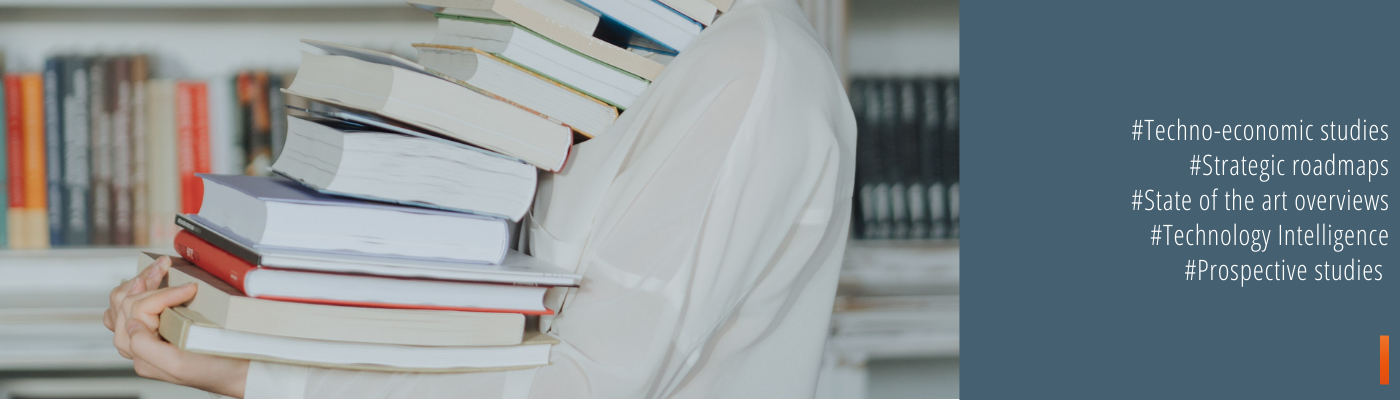
Our documents
Latest documents
Report/Decarbonation of cooking and drying processes - part II
Category : Resume Published on19/06/2025
Activity : Études pour les adhérents
Description :
This study focuses on decarbonising drying and cooking processes. It is a direct follow-up to another ALLICE study of the same name. Three types of decarbonisation solutions are examined: energy efficiency, electrification and the use of renewable and recovered energy sources. The study aims to examine the application of these solutions in three case studies and compare the energy, economic and environmental results up to 2050.
The applications studied are glass annealing lehrs, metallurgical tempering furnaces and starch drying systems. An initial energy efficiency solution has been implemented for all three cases. This is considered a prerequisite for the use of carbon-free energy. It is widely accepted that carbon-free energy can only become widespread if energy consumption is reduced. Based on this initial development, several alternative energy solutions are then studied on a case-by-case basis : hybridisation, electrification, solar, geothermal, hydrogen and biomass.
Overall, two trends emerge from all the case studies.
- Firstly, energy efficiency consistently ranks as one of the most economically attractive solutions. This is only challenged by electrification solutions offering additional benefits or renewable energy sources at highly competitive prices, such as geothermal energy.
- Secondly, electrification is consistently one of the solutions offering the greatest reduction in CO₂ emissions. However, it often generates the least profitable returns. At the same time, there are often renewable energy solutions with a similar impact on GHG emissions that are more economically attractive.
This study shows that all solutions can significantly reduce GHG emissions. To further reduce GHG emissions linked to certain processes or specific cases, CCUS solutions may be necessary (Carbon Capture, Utilisation and Storage). Finally, it is important to consider the other environmental impacts of the processes, particularly with regard to water usage.
Areas of expertise : Decarbonisation at a glance
Activity : Veille
Description :
Areas of expertise : Decarbonisation at a glance
Activity : Veille
Description :
Areas of expertise : Decarbonisation at a glance
Activity : Animation de la filière
Description :
Areas of expertise : Decarbonisation at a glance
Potential for electrification of industrial thermal processes
Category : Report Published on28/03/2025
Activity : Veille
Description :
The maximum theoretical potential for electrification is 29% by 2035. Other decarbonisation solutions must therefore be considered, and the integration of decarbonised gas appears to be a strategic and complementary alternative when electrification is not relevant. In this context, a sharp increase in the consumption of decarbonised gases in industry is expected, particularly for certain very high-temperature processes, especially in the terracotta and steel sectors. Feedback on the integration of decarbonised gases in industrial processes is already available.
In the future, the place of each of these gases and their level of penetration will depend on the evolution of the production sectors, the level of support for these sectors, as well as the technological choices made for each of the other French energy uses. For example, boilers will be able to more easily accept raw gases such as biogas or syngas. On the other hand, the use of decarbonised gases in ovens is more complex, but there is greater interest in their use for cooking.
Areas of expertise : Decarbonisation at a glance
State of the art High Temperature Heat Pump - part 2
Category : Resume Published on25/03/2025
Activity : Études pour les adhérents
Description :
In 2021, ALLICE carried out an initial technical study on very-high-temperature heat pumps for industry. This study reviewed the state of the art of existing solutions and analysed in detail three heat pump technologies considered particularly relevant for the industrial sector. In order to deepen this analysis, ALLICE launched three new studies in 2024 aimed at identifying the obstacles and levers to the deployment of these technologies.
This second study updates the work carried out in 2021 on Heat Pumps by incorporating the latest technological advances (R&D, feedback). It focuses on three alternative technologies:
- Stirling engine helium heat pumps
- Thermoacoustic heat pumps
- Coupling a ‘conventional’ heat pump with mechanical vapour compression (MVC).
The study also lists demonstrators and pilot projects in Europe.
It is followed by a section 3 dedicated to the technological integration of heat pumps for industry.
Areas of expertise : Energy Efficiency
Study/ Technological integration of heat pumps - part 3
Category : Resume Published on25/03/2025
Activity : Études pour les adhérents
Description :
In 2021, ALLICE carried out an initial technical study on very-high-temperature heat pumps for industry. This study reviewed the state of the art of existing solutions and analysed in detail three heat pump technologies considered particularly relevant for the industrial sector. In order to deepen this analysis, ALLICE launched three new studies in 2024 aimed at identifying the obstacles and levers to the deployment of these technologies.
The third study completes the other two studies by identifying the key factors (barriers, obstacles, levers) influencing the implementation of heat pumps on industrial sites, from a technical, practical, economic and regulatory point of view.
A modelling tool has been developed to illustrate the results of the study, highlighting the impact of various parameters on the performance of heat pump projects.
This tool helps to anticipate favourable or unfavourable configurations according to technical and economic criteria, and is available to members.
Areas of expertise : Energy Efficiency
Market study on mature Heat Pump technologies - part 1
Category : Resume Published on20/03/2025
Activity : Études pour les adhérents
Description :
In 2021, ALLICE carried out an initial technical study on very high-temperature heat pumps (PAC THT) for industry. This state of the art of existing solutions and analyses in detail three heat pump technologies considered to be particularly relevant for the industrial sector. In order to deepen this analysis, ALLICE launched three new studies in 2024 aimed at identifying the obstacles and levers to the deployment of these technologies.
This study corresponds to Part 1: ‘Market study on mature heat pump solutions in industry’. It is followed by a section 2 on the state of the art in heat pumps, and then a a part 3 dedicated to the technological integration of heat pumps for industry.
Despite their benefits in terms of energy and decarbonisation, heat pumps are struggling to be deployed on a large scale in industry. The aim of part 1 of the study is to analyse the conditions necessary for their adoption. In particular, it aims to understanding the current market, identifying the relevant target sectors that could use this technology as a solution to decarbonisation solution, and identifying the levers and business models that could likely to stimulate the deployment of Heat Pumps in industry.
Areas of expertise : Energy Efficiency
Flue gas treatment as a means of industrial heat recovery
Category : Resume Published on12/02/2025
Activity : Études pour les adhérents
Description :
Energy recovery from polluted flue gases concerns a large number of industries that emit waste heat, particularly in the food industry (ovens, frying, cooking, drying), the materials industry (lime, tiles and bricks, insulation, glass) and the metal and mechanical engineering industries (painting lines, smelting, heat treatment).
This study presents the state of the art in flue gas treatment solutions alone, but also in treatment solutions that include heat recovery.The focus is on seven exchanger technologies, the advantages and disadvantages of which have been summarised in technology sheets. Some have already been analysed in previous ALLICE work, while three are the subject of new sheets for in-depth evaluation :
- Exchanger cascade with flue gas treatment
- Glass exchangers for acid gases
- Polymer exchangers for low temperature polluted flue gases
In order to enrich these sheets with data from the actual operation of flue gas treatment systems, the study includes three feedback:
- Flue gas treatment and heat recovery in an oil/natural gas refinery
- Flue gas treatment with heat recovery in the brick industry
- Flue gas treatment with heat recovery in a waste incineration plant
Areas of expertise : Energy Efficiency
Barriers and levers to the deployment of high-temperature heat storage in industry
Category : Resume Published on23/01/2025
Activity : Études pour les adhérents
Description :
In 2021, ALLICE carried out an initial technical study on the heat storage in industry, presenting a state of the art of existing solutions as well as several case studies evaluating the technical feasibility of implementing these solutions. There is interest in thermocline technologies on the part of most thermal storage for solid thermocline technologies. This interest has accelerated the maturity of this technology, which is now on the market with a TRL of 8.
Detailed fact sheets for each of the technologies are included in the study report.
Today, although heat storage projects offer advantages in terms of energy performance, their deployment seems to be running into difficulties. This raises questions about the target market for these solutions and the business models that could accelerate their adoption. Thermal storage capacities deployed in industry remain limited.
The aim of this study is therefore to analyse the conditions necessary for the deployment of heat storage in industry. This includes :
- understanding the current market
- identify the relevant sectors for implementing the technologies;
- identifying the levers and economic models likely to stimulate the deployment of heat storage in industry.
The study focused on industrial applications involving heat storage + high-temperature recovery (above 150°C). Analysis of coupling with a power-to-heat solution was also considered.
Areas of expertise : Energy Efficiency